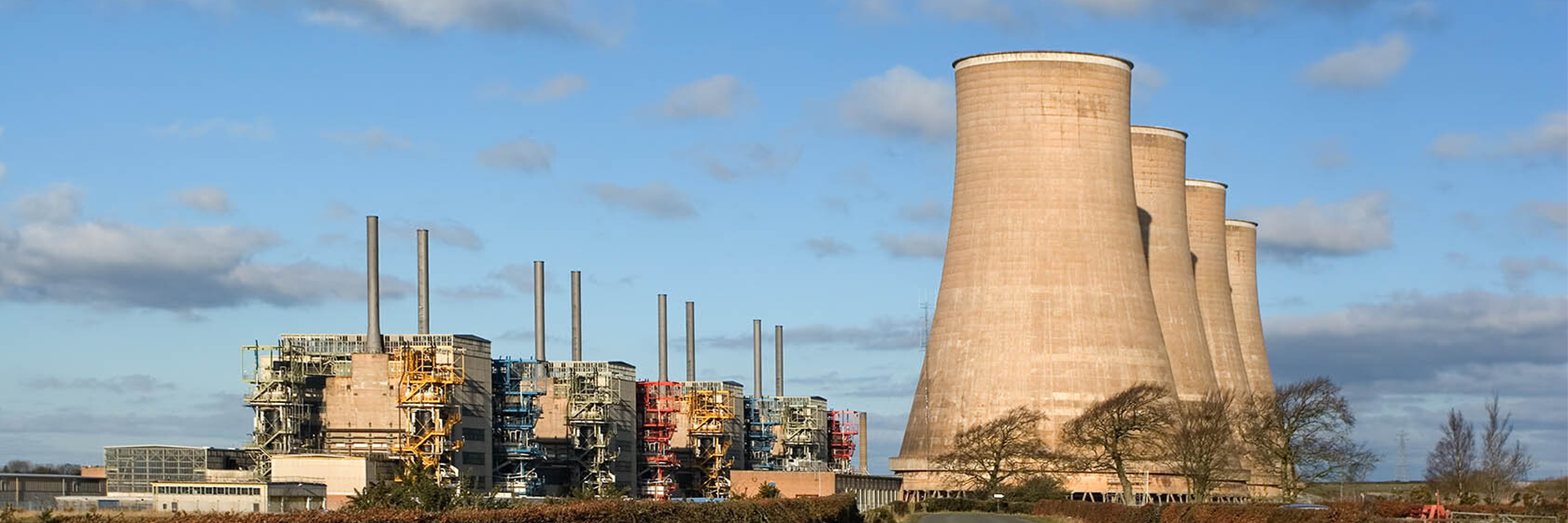
PIPESTRESS is a complete calculation system for nuclear and non-nuclear piping codes. It has been continuously maintained in accordance with nuclear QA procedures for more than 40 years. Several major nuclear engineering organizations use PIPESTRESS as their principal piping analysis program. The software has been used by engineering organizations all over the globe to analyze piping in more than 50 nuclear power plants…..
Advanced Modeling
PIPESTRESS has the capability to model very large structures and complex loadings with up to 900 userdefined load and combination cases. It includes a complete set of piping elements and supports including straight pipes, elbows, miter bends, expansion joints, flanges, linear and non-linear restraints with gaps and friction, spring hangers, snubbers, etc. In addition, you can model beam elements with a non-prismatic cross-section.
Static Analysis
By using PIPESTRESS you have access to an extensive set of static loads: operating and test weight, thermal expansion, snow and wind, settlement, cold springing, variable pseudo-static acceleration, applied support movements, variable fluid density, uniform and trapezoidal loads, horizontal and non-horizontal stratification effects.
Dynamic Analysis
PIPESTRESS offers advanced dynamic capabilities for floor response analysis and time history analysis. Increase the precision of your calculations by enabling the rigid mode correction (“left-out-force†method), avoid unnecessary conservatism by calculating the displacements, rotations and accelerations in user-defined local coordinates, define the most complex loads with up to 3800 independent support levels, compensate uncertainties of the modal extraction by enabling the shift option, and use the strain energy weighted composite modal damping defined in ASME-1233.
Buried Piping
Benefit from simplified workflows with automatic soil spring generation. Springs can be either elastic (as per ASME B31.1 Appendix VII) or elastic-plastic (as per ASCE code). An integrated soil calculator provides easier modeling workflows in accordance with ASME B31.1 App. VII.
Flange Calculation
Flange modules automatically retrieve results of piping analysis and input them in flange verification, according to codes EN 13480, ASME III and RCC-M, and various methods (equivalent pressure, Taylor Forge, etc.)